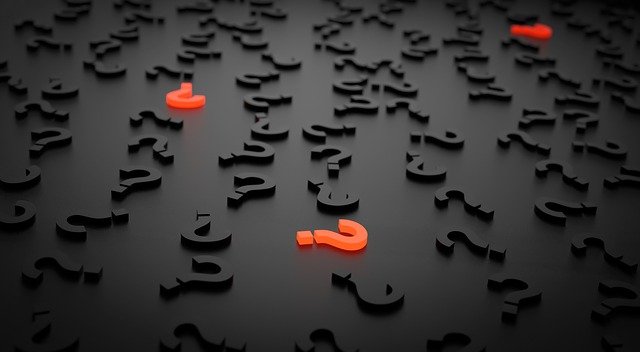
En mantenimiento industrial se pueden utilizar una serie de técnicas para gestionar el mantenimiento con el fin de mejorar el funcionamiento de las instalaciones y la organización. Teniendo presente que todo es mejorable el método Kaizen se basa en realizar pequeñas mejoras de manera continua.
Para aplicar este método y conseguir resultados es muy importante implicar al colectivo, desde la dirección hasta los operarios pasando por la sección de mantenimiento.
La palabra Kaizen es japonesa y su significado es Kai=cambio Zen=Bueno, aunque el concepto está asociado a la mejora con lo que es conocido por «cambio para mejorar» o «mejora continua». El método Kaizen se produjo en Japón por la necesidad de mejorar los procesos productivos de la industria japonesa, en concreto en la industria automovilística de Toyota, orientando al cliente la mejora de calidad, mejora de la productividad, eliminando pasos que no aporten valor al producto.
Con el tiempo el método Kaizen ha sido muy estudiado y documentado. En su origen fue utilizado en la industria automovilística. En la actualidad es aplicado para diferentes sectores, incluyendo en el desarrollo personal.
Relacionado con el desarrollo personal o simplemente como curiosidad, al indicar muchos datos de diferentes estudios, recomiendo escuchar el podcast de Jaime Rodriguez De Santiago, este podcast me suelen acompañar en los trayectos en coche al trabajo aprendiendo algo nuevo cada día.
Web de Jaime Rodriguez De Santiago donde encontrar enlaces a los podcasts de Kaizen
El principio de funcionamiento del modelo Kaizen se basa en la mejora continua de manera organizada, dando pequeños pasos en el proceso de mejora.
El método Kaizen aplicado a la industria se dividen en siete sistemas:
1.- Sistema de producción Toyota JIT( Just In Time): Se basa en eliminar los sobrecostes producidos por stock que no circula tanto de producto elaborado como por elaborar.
2.- Gestión de la Calidad Total (TQM): Garantiza la calidad Total evitando repetir procesos o desechar productos por defectos de calidad.
3.- Mantenimiento Productivo Total (TPM): Este sistema de mantenimiento ayuda a la máxima capacidad de las maquinas para obtener la máxima producción con la mejor calidad. Para saber más sobre Mantenimiento Productivo Total puede leer este articulo TPM
4.- Sistema participativo de Grupos de Trabajo: El personal organizado en grupos de trabajo pequeños encargados de la resolución de problemas.
5.- Sistema de Sugerencias: Aprovechando los conocimientos y experiencia del personal se crea una manera de recepción de ideas de posibles mejoras.
6.- Plena participación en la planificación, control y Evaluación del proceso de funcionamiento: Se implica a toda la empresa desde directivos hasta el ultimo operario para organizar la empresa en busca de su mejora continua.
7.- Sistema de Costos Japonés: Sistema de reducción de costes, controlando las fallas, desperdicios generados en la producción.
Dejar una contestacion